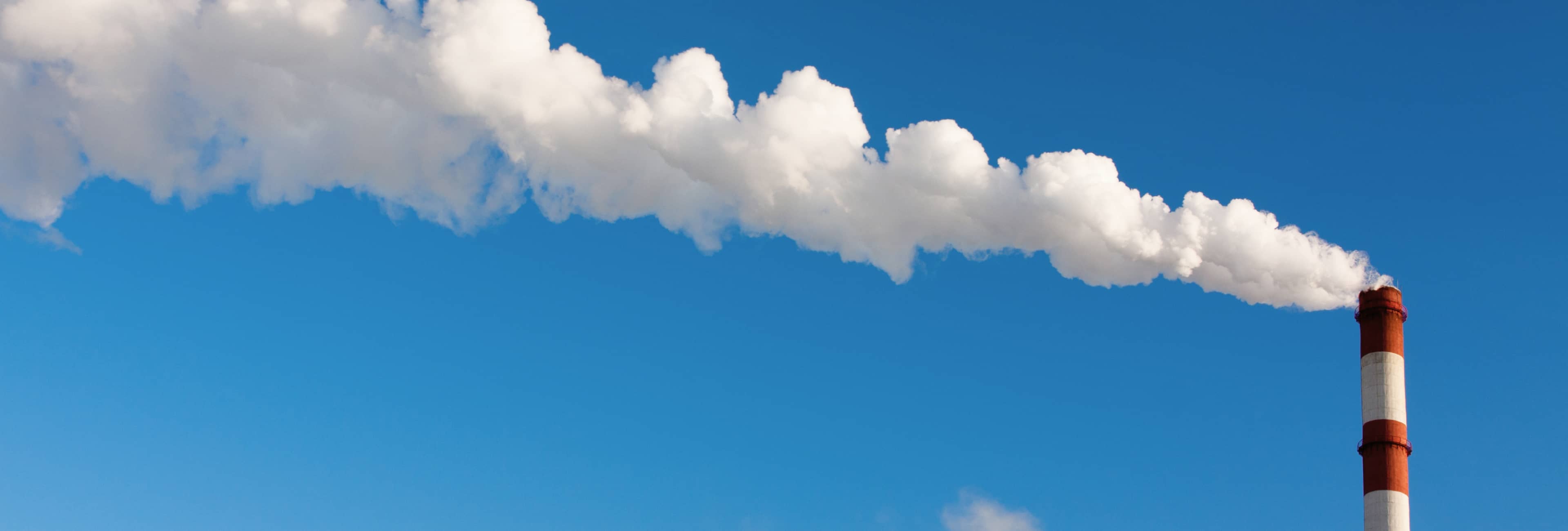
Governments and environmental organisations are taking severe measures against factories that operate erratically and imposing significant fines. In 2021, the EPA's civil enforcement program assessed $1.05 billion in penalties for noncompliance with environmental laws. Green policies have also forced major polluting industries, such as the energy sector, pharma, agriculture and others, to measure and record air emissions more accurately and continuously.
The EU's Large Combustion Plant Directive (LCPD) stipulates that power plants with a thermal energy output of more than 50 megawatts must constantly measure gas emissions. According to the LCPD, a maximum of ten days' worth of emission data may be lost in one year, including days required for maintenance.
The importance of having efficient and reliable tools for acquiring emission data from a plant owner's perspective cannot be understated. Environmental constraints can not only affect production but failing to provide emission values for extended periods may result in an authority-imposed plant shutdown.
Heavy reliance on hardware-based equipment and manual labour have been the traditional approaches to pollution levels management. However, predictive emissions monitoring systems are one possible solution that businesses are investigating as an alternative.
What is a predictive emissions monitoring system (PEMS)?
A predictive emissions monitoring system, or PEMS, is a system that uses existing process data and statistical methods to predict discharges from a manufacturing process. It uses a combustion facility's operating parameters to build a model that can predict emissions through the first principle, statistical or machine learning methods.
In various applications, PEMS replaced Emissions Monitoring Systems or Continuous Emissions Monitoring Systems (CEMS). PEMS can accurately predict environmental emissions, such as NOx, CO, CO2, and SO2, from gas or oil-fired boilers, reformers, or gas turbines without the need for actual hardware analysers known as CEMS.
Predictive emissions monitoring systems provide real-time data on hazardous waste. This information can identify problems early on and take corrective action before pollution levels exceed legal limits. A PEMS can help plant or factory owners meet their emissions targets more efficiently by constantly monitoring and adjusting the strategy.
Three methods behind the development of PEMS software
PEMS uses sophisticated computer algorithms that utilise artificial intelligence and machine learning. The methods used to develop PEMS can be broadly classified into three main categories.
1. The first principle method
It is based on analytical physical equations from the fields of thermodynamics, kinetics, mass and energy balance. The parameters in the equations can be adjusted to get an exact correspondence between operation information and corresponding emissions.
2. Statistical method
This method quantitatively predicts emissions based on relationships it finds between key industrial processes and resulting polluting substances.
3. Machine learning method
This method employs machine learning services and techniques to build highly accurate predictive models based on operating parameters. Artificial neural networks (ANNs) are machine learning algorithms that are most commonly used for developing a predictive emissions monitoring system.
As opposed to the statistical method, machine learning uses learning algorithms to find patterns in historical paired operating and emissions data, which can then be used to predict future pollution levels. PEMS is among the earliest examples of AI applications for environmental monitoring.
Both statistical and machine learning methods use historical information to develop prediction models. Some even combine the two methods into one category, called the data-driven method.
The benefits of predictive emissions monitoring system
PEMS can provide significant advantages over traditional manual monitoring methods, including improved accuracy, increased efficiency, and reduced costs. Here are some key benefits:
- Enhanced accuracy. PEMS uses advanced data analysis techniques to provide more reliable emissions data than traditional manual monitoring methods. This improved accuracy can help facility operators make better pollutants control and compliance decisions.
- Better performance. PEMS can automate many tasks associated with manual emissions monitoring, including information collection, analysis, and reporting. This can free up staff time for other tasks and improve the overall efficiency of the emissions monitoring process.
- Seamless installation. PEMS does not require complex infrastructure to collect the sample at the stack and handle. It can be directly connected to plant control systems without the need for additional components and no shut down required.
- Lower expenditure. PEMS can reduce the costs associated with emissions monitoring by eliminating the need for manual data collection and analysis. Additionally, PEMS can help facilities to avoid costly fines and penalties for exceeding discharge limits.
- Backup system. PEMS can serve as a backup for CEMS systems. By helping to identify possible malfunctions and providing alternative measurements when analysers are in maintenance, PEMS can play an essential role in ensuring accurate readings.
Conclusions
In the ever-changing field of environmental protection and management, the role of technology in improving the predictability of violations and reducing their impact has an increasingly important role.
Predictive emissions monitoring system is a huge step forward in air pollution control. The key benefits of PEMS are its ability to accurately predict the emission of hazardous gases, its ease of use and the improved efficiency it brings. Additionally, the system can provide information that can help the development of new and more effective emission control strategies.